- 50mm of fine sand
- 2.7 kg of Soiltex Geofiber White (fine white fibre) per square meter
- 1.6 l of Soilworks Durasoil per square meter
Due to delivery timing issues we had to put down the sand, then spread the fibre on top. To mix the sand and the fibre we used a rotary hoe. The one we selected was a self propelled unit from a local hire shop and we spent nearly a day mixing the sand and the fibre. Finally we added the Durasoil on top, which we applied with a watering can; ideally we would have sprayed it on the surface, unfortunately the Durasoil was too viscous for our spray unit.
Our key concerns when designing our surface:
- Dust control - indoors are notoriously dusty and dust can quickly turn a pleasant working session into something neither horse nor rider want to go on with
- ‘Low’ maintenance - there is no such thing as a maintenance free arena, and time spent maintaining the arena is time spent away from the horse. However, there are some activities that we don’t mind as much as others. In our case, we are prepared to put more time into levelling the arena.
- Footing - we wanted a shock absorbing footing, that was not too deep, solid enough and not slippery for cavaleti and show jumping
- Water - as we only have the water we collect from the roof of the arena available, we wanted a surface that did not require significant watering (also watering arenas can be very time consuming)
The surface is rather shallow and does require regular rolling to ensure that base remains completely covered. It is also more difficult to construct a shallow surface (50mm over 20m requires high accuracy - even with laser levelling - when putting the materials down) when compared to a deeper surface.
Geofiber White
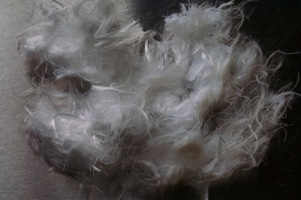
Geofiber White with Fine Sand and Soilworks Durasoil
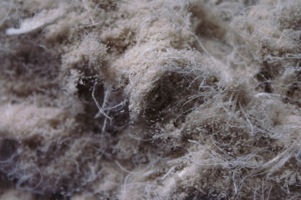
Useful Techniques
Putting the sand out was a major part of the surface preparation as the sand was delivered directly from the quarry (where it was made and washed). Each load was directed to a specific point within the arena and the truck pulled forward to spread the sand out as evenly as possible. After all the sand was delivered the surface was laser levelled with a dingo. By carefully spreading the sand with the truck a lot of time can be saved in the levelling operation.
To ensure that we spread the fibre evenly over the surface we weighed out the fibre in blue Ikea bags using a fishing scale and the strewed them over marked out meter square areas on the arena.
Similarly, we measured the amount of dust control liquid out into watering cans and then spread it over marked out meter square areas.
Because we were working with a relatively thin surface on a fairly unforgiving base we applied a lot more manual effort than if the base had been made of a levelled coarse sand as suggested in the Soiltex literature. In particular, the hand controlled rotary hoe required considerably more effort than one mounted on a tractor.
Maintenance
The sand fibre mix is rolled regularly (typically after every second working session) to help level the surface and maintain compaction.
In Use
The surface has been down for 6 months (March 2010) and has not needed watering. Prior to adding the Durasoil the arena needed 20 minutes of watering with a fire hose before each ride and additional watering during summer to maintain a reasonable working consistency and dust level. Since adding the dust suppressant the surface has improved as the Durasoil acts also as a binder holding the fibre and sand together.
Renewal
After having the surface down over 2.5 years (February 2012) we have put down the second batch of Durasoil at the 2/3 top up rate.
Australian Suppliers
The sand used was FINESA from Rocla (http://quarry.rocla.com.au), the Soitex Geofiber White fibre was supplied by Capricorn Australia (http://www.equineproducts.com.au) and the Durasoil was supplied by Yanmar Soil (http://www.yanmarsoil.com.au)