3018 Mill
23/09/21 15:03 Filed in: Milling
I recently purchased a 3018 Pro mill to learn a bit about CNC milling (ironically its my second mill, I have a tiny Roland mill that I was going to use for PCB milling but ended up having too many software issues with). The intention was to mill some trivial PCBs, a bit of signage and perhaps some laser engraving.
So I purchased a basic 3018 pro with a laser module.
Some key learnings emerged (spoiler alert there is still a long way to go)
So I purchased a basic 3018 pro with a laser module.
Some key learnings emerged (spoiler alert there is still a long way to go)
In Use
The first thing to note is that 3D printing is way easier than milling. Materials are more consistent and better behaved.
The machine
The 3018 Pro is a pretty basic machine and there is no bedd levelling adjustment, apparently you just level your spoiler board.
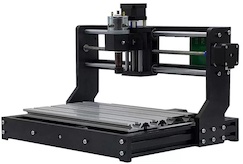
Surprisingly it works pretty well. Reasonably accurate and plenty of people who have shared their experiences about using it. (Shout out to James Dean Designs for his series of videos)
But the basic machine really needs a few upgrades before using it.
Upgrades
Emergency stop switch
You will want at least one of these. I have 2: one inside the enclosure and one outside the enclosure.
Sooner rather than later you will want to stop the machine doing something bad and even with the 10k RPM spindle bad is easy to achieve. Classic bad things include:
- trying to drill your work surface
- trying to move the machine outside its operating area
- forgetting to start the spindle and trying to mill (very bad for the bits)
The big red physical button is your friend. Don't be fooled into thinking you will find the stop button in you software interface in time.
Enclosure
Milling is loud and messy. You are cutting material and the remains have to go somewhere. Enclosing it is going to make your life less easy but a whole lot more pleasant in the long run.
I bought an acrylic enclosure and made a base plate from acrylic and the dust is all contained. Issues with the enclosure are:
- can limit your work area if you allow materials to extend beyond the table
- this enclosure's magnetically removable front is going to have the magnets replaced as they don't stick well enough to the aluminium and acrylic
- you will want to be able to get access to the machine so the enclosures need to be easy to remove
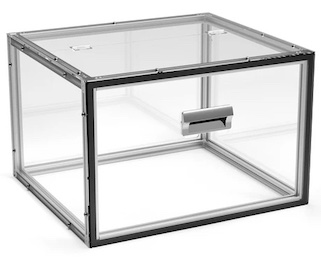
Cable management
Cables getting snarled in moving parts is a bad idea. You will want to wrap them up with spiral wrap at the minimum.
Limit switches
Some people argue you don't need these. My experience is that it is in line with Murphy's Law (You will try to go outside the machine's working area)
Software
Mac software is available for the GRBL boards used by this machine but windows software is easier to come by.
Currently I am using:
- Candle to drive the machine but you will have to compile it yourself.
- Carbide Create will let you create 2.5D designs fairly easily.
- Camotics simulates tool paths
Candle and Camotics have Linux versions - which may end up being preferable for driving the machines
What I should have done
Given the level of upgrades that I had to do before I was happy with using the machine. The more expensive model 3018 Prover model which includes limit switches, emergency stop and cable wrapping would actually have been more economical (slightly less fun as I manufactured my own limit switch and emergency stop button designs)
More to come
Currently I am machining MDF spoil boards before doing some engraving and doing some very basic PCBs (basically single sided supports for switches). My strong feeling is that if your circuit is even slightly complex the compromises required to mill the board are not worth it unless you need it right now. But more on that in future.